Video:
YouTube Video (starting @ 9m 26s) showing the heatsink and compound issue.
Let me preface this by saying the blame is NOT with Apple's engineers. I understand and absolutely applaud their methodology and execution in the Macbook Pro line.
However, Apple's manufacturing and assembly need help.
We're going to go into why:
Apple's machine work on the heatsinks is sub-par, immediately causing poor contact, and thus poor heat transfer from the CPU/GPU to the heatsink.
This is compounded with entirely too much heatsink compound on the dies.
First, a little information that seems to be *sorely* lacking in the Apple community (some materials engineering):
The very best heat transfer method is direct metal-to-metal contact. Unfortunately, once you separate a piece of metal into two pieces, you will always have air between the two pieces, due to surface imperfections.
Now, if you were to look at a flat piece of metal under a microscope, you would see this:
See those valleys, dips, mountains?
Now notice the roughness average (known in the industry as RA) values.
The roughness average of a polished mirror finish is usually 3-5 microinches. That NiTi 80 has an RA of 1 micron (1 micron = ~39 microinches), and you see the valleys and mountains.
Here is an image of a proper heatsink base (Taken from Swiftech's website):
Do you see how reflective the surface is? That means there are very few valleys. I'd say that Swiftech heatsink has an RA of 3-5 microinches.
When I pulled the heatsink out of my Macbook Pro, I was astounded. While I don't have a profilometer available, I'd estimate the RA of the heatsink copper pads in the neighborhood of 40-60 RA. That's freaking pathetic in a system that you pay the kind of money you do for a quality Macbook Pro. I've seen better heatsink bases in a DELL for crying out loud. Now, my lapping was not the best job in the world. I may have gotten the RA down to the 25 range, but it certainly helped.
If you'd like to read more on surface finishes, check out Wikipedia. Plenty of reading, and you can start doing some thinking on your own - Surface Finish
So what the heck does that have to do with all the heatsink goop I see spread around like peanut butter on a sammich? (mmm sammich - sorry, I'm hungry) Glad you asked!
Direct metal to metal is the best heat transfer mechanism, as we've already stated, but we have those surface imperfections that we can't even see to deal with.
Enter: heatsink compound.
See, air is a great insulator; air does not allow heat to transfer effectively. We use heatsink compound of low thermal resistance to 'fill in' those little valleys and imperfections, so we don't have air keeping our heat transfer at bay.
The normal white stuff you see is usually a ZnO (zinc oxide) mixture. And yes, it does the job. However, something like Arctic Silver works even better at facilitating that heat transfer (pure silver is about 10x as thermally conductive as ZnO), so we can move that heat out of the CPU and into the heatsink system.
That's also why it is SO important to have AS LITTLE HEATSINK COMPOUND AS POSSIBLE to fill those voids in the metal-to-metal contact patch. Copper is about 9x as thermally conductive as ZnO, so having too much heatsink compound hurts thermal transfer rate.
To reiterate, this is *not* the fault of Apple's engineering team. The heatpipe assembly is good, the fan control is good, the exhaust system is... well, ok, I think they could have done better there, honestly, but they did the best they could within those design parameters.
Under normal conditions that most use their fashionable Macbooks in, the raw heatpipe transfer will keep the laptop CPU/GPU under ~120F (49C). Heck, I have 11 tabs open in Chrome (one of which is Youtube, my channel actually) and carrying on a couple conversations in both Adium and Colloqey, and I'm sitting at 106F (41C) temperatures at the moment.
The CPU will remain clocked down, the discrete GPU stays off, and things are great.
Now, once you start pushing things, (such as encoding a 40+ minute 1080p Youtube video) CPU clocks come up, discrete GPU comes online and clocks up, and yes, heat starts getting really generated. Fans start ramping up to keep up with the thermal demands, exhaust gets blown out the hinge area, and away we all go.
I have hit 201F (94C) while doing these full power encodes, and once the fans are up and running (5500rpm, not even full 6200rpm) temperatures tend to stabilize around 185F (85C), which I imagine is right where the engineers want it maxed at around. If I pop the Macbook Pro up on a 1" thick book so the exhaust area has more room to 'breathe' and push the fans to 6200rpm, I can get my temps down to 175F (79C) while does those full encodes. I have no thermal throttling at any time for any thing.
Let me also mention that I have the BTO 2.5Ghz Quad i7 - NOT the normal 2.2 or 2.4 Ghz versions.
Whomever Apple has manufacturing their heatsinks, seriously needs to get on the ball with providing a properly machined surface to attach to the logic board.
Whomever Apple has assembling the laptops, needs to learn how to properly apply heatsink compound.
Combine too much heatsink compound with poor heatsink machine work, and you know what you have?
A Macbook Pro that runs too damn hot.
I hope this was helpful for you all. Questions? Comments? Keep your blind fanboy-ism, but constructive discussion, I'm all for.
*edit* Micron to microinch conversion - my fault. Used to dealing with µin, not µm
YouTube Video (starting @ 9m 26s) showing the heatsink and compound issue.
Let me preface this by saying the blame is NOT with Apple's engineers. I understand and absolutely applaud their methodology and execution in the Macbook Pro line.
However, Apple's manufacturing and assembly need help.
We're going to go into why:
Apple's machine work on the heatsinks is sub-par, immediately causing poor contact, and thus poor heat transfer from the CPU/GPU to the heatsink.
This is compounded with entirely too much heatsink compound on the dies.
First, a little information that seems to be *sorely* lacking in the Apple community (some materials engineering):
The very best heat transfer method is direct metal-to-metal contact. Unfortunately, once you separate a piece of metal into two pieces, you will always have air between the two pieces, due to surface imperfections.
Now, if you were to look at a flat piece of metal under a microscope, you would see this:

See those valleys, dips, mountains?
Now notice the roughness average (known in the industry as RA) values.
The roughness average of a polished mirror finish is usually 3-5 microinches. That NiTi 80 has an RA of 1 micron (1 micron = ~39 microinches), and you see the valleys and mountains.
Here is an image of a proper heatsink base (Taken from Swiftech's website):
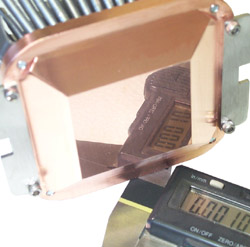
Do you see how reflective the surface is? That means there are very few valleys. I'd say that Swiftech heatsink has an RA of 3-5 microinches.
When I pulled the heatsink out of my Macbook Pro, I was astounded. While I don't have a profilometer available, I'd estimate the RA of the heatsink copper pads in the neighborhood of 40-60 RA. That's freaking pathetic in a system that you pay the kind of money you do for a quality Macbook Pro. I've seen better heatsink bases in a DELL for crying out loud. Now, my lapping was not the best job in the world. I may have gotten the RA down to the 25 range, but it certainly helped.
If you'd like to read more on surface finishes, check out Wikipedia. Plenty of reading, and you can start doing some thinking on your own - Surface Finish
So what the heck does that have to do with all the heatsink goop I see spread around like peanut butter on a sammich? (mmm sammich - sorry, I'm hungry) Glad you asked!
Direct metal to metal is the best heat transfer mechanism, as we've already stated, but we have those surface imperfections that we can't even see to deal with.
Enter: heatsink compound.
See, air is a great insulator; air does not allow heat to transfer effectively. We use heatsink compound of low thermal resistance to 'fill in' those little valleys and imperfections, so we don't have air keeping our heat transfer at bay.
The normal white stuff you see is usually a ZnO (zinc oxide) mixture. And yes, it does the job. However, something like Arctic Silver works even better at facilitating that heat transfer (pure silver is about 10x as thermally conductive as ZnO), so we can move that heat out of the CPU and into the heatsink system.
That's also why it is SO important to have AS LITTLE HEATSINK COMPOUND AS POSSIBLE to fill those voids in the metal-to-metal contact patch. Copper is about 9x as thermally conductive as ZnO, so having too much heatsink compound hurts thermal transfer rate.
To reiterate, this is *not* the fault of Apple's engineering team. The heatpipe assembly is good, the fan control is good, the exhaust system is... well, ok, I think they could have done better there, honestly, but they did the best they could within those design parameters.
Under normal conditions that most use their fashionable Macbooks in, the raw heatpipe transfer will keep the laptop CPU/GPU under ~120F (49C). Heck, I have 11 tabs open in Chrome (one of which is Youtube, my channel actually) and carrying on a couple conversations in both Adium and Colloqey, and I'm sitting at 106F (41C) temperatures at the moment.
The CPU will remain clocked down, the discrete GPU stays off, and things are great.
Now, once you start pushing things, (such as encoding a 40+ minute 1080p Youtube video) CPU clocks come up, discrete GPU comes online and clocks up, and yes, heat starts getting really generated. Fans start ramping up to keep up with the thermal demands, exhaust gets blown out the hinge area, and away we all go.
I have hit 201F (94C) while doing these full power encodes, and once the fans are up and running (5500rpm, not even full 6200rpm) temperatures tend to stabilize around 185F (85C), which I imagine is right where the engineers want it maxed at around. If I pop the Macbook Pro up on a 1" thick book so the exhaust area has more room to 'breathe' and push the fans to 6200rpm, I can get my temps down to 175F (79C) while does those full encodes. I have no thermal throttling at any time for any thing.
Let me also mention that I have the BTO 2.5Ghz Quad i7 - NOT the normal 2.2 or 2.4 Ghz versions.
Whomever Apple has manufacturing their heatsinks, seriously needs to get on the ball with providing a properly machined surface to attach to the logic board.
Whomever Apple has assembling the laptops, needs to learn how to properly apply heatsink compound.
Combine too much heatsink compound with poor heatsink machine work, and you know what you have?
A Macbook Pro that runs too damn hot.
I hope this was helpful for you all. Questions? Comments? Keep your blind fanboy-ism, but constructive discussion, I'm all for.
*edit* Micron to microinch conversion - my fault. Used to dealing with µin, not µm
Last edited: